REGULATION OF THE EUROPEAN PARLIAMENT AND OF THE COUNCIL
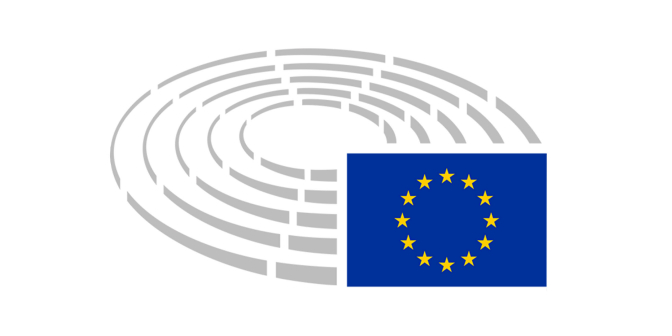
This document describes in abbreviated form the content of this EU regulation with regard to the GENEREX products BACS, SMARTBATTERY and SMARTLOGGER and their use in stationary energy storage systems.
Demand for batteries is forecasted to increase 19-fold in the coming years; such exponential demand lends an increasing strategic weight to the industrial and stationary battery markets. Significant scientific and technical advances will continue to be made in the field of battery technology, and in order to best shepherd such advances towards a sustainable and positively lasting impact it has proven necessary to create a harmonized regulatory framework for the entire life cycle of batteries placed on the market in the EU.
For this reason, on December 10, 2020, the European Commission published a proposal for the new Battery Regulation with the goal of repealing the Battery Directive 2006/66/EC and amending Regulation 2019/1020.
As a part of this new regulatory framework, by Jan. 1, 2026 the EU will require that rechargeable industrial and traction batteries include a battery management system.
The whole documentation can be found here, for further reading: https://eur-lex.europa.eu/legal- content/EN/TXT/HTML/?uri=CELEX:52020PC0798&from=EN
Particularly of relevance is Article 14, Chapter III, wherein the role of a Battery Management System is outlined.
As stated in the legislation documentation, a 'battery management system' is an electronic component that monitors and controls the electrical and thermal functions of the battery, manages and stores data on the parameters for determining the ageing state and expected lifetime of batteries, and communicates with the device in which the battery is installed.
According to the EU Council, a “battery management system” must fulfill or otherwise provide necessary data measurement according a framework of key parameters. These parameters, and their relationship to GENEREX’s BACS product family, are as follows:a
Battery Capacity
- Remaining Capacity - BACS: As of 2022 BACS is able to calculate and display individual cell/battery capacity in real-time.
- Remaining Battery Efficiency – also known as “Round Trip Efficiency”, this is determined through a direct comparison between 2 distinct discharges. BACS: The difference between the two discharges shown by the BACSVIEWER REPORT functionality represents the efficiency, which decreases with age and number of discharges.
- Battery Capacity: The value of AC / DC resistance should be plotted against the available capacity of the cell as determined by the discharge. The available capacity should be expressed as a percentage of nominal capacity. BACS is the only BMS on the market which displays the battery capacity against the AC/DC resistance (and includes Battery Current and Temperature in the Capacity measurements).
- Total Capacity Loss – The total capacity loss of a given cell is calculated by comparing the difference between the nominal capacity of the battery when new against the result of a recent discharge test. BACS: Through use of the BACSVIEWER software such a comparison is straightforward and readily accessible.
- Remaining Power Capacity and Power Loss – These values are determined from the given cell "Battery Capacity" as compared to the first recorded discharge at start-up. BACS: Ensures a 100% state of charge for each battery thus providing the prerequisite for comparability of discharge tests. The long term data as provided in tandem with BACSVIEWER allows for a quick and efficient determination of lifespan power loss.
- Autonomy time: The capability of the battery to give its design run time at the claimed power level is a very important characteristic for the user. The direct way to determine this capability is to perform a capacity test, but this will only establish the autonomy time capability at the time of the test. Capacity testing is however undesirable in a monitoring environment, and estimates of autonomy will have to be derived from load tests or AC /DC resistance characteristics. BACS provides a calculation of autonomy time based on the relationship between UPS input, battery current, battery voltage and temperature and impedance.
- Battery Capacity determination by discharge tests: Discharging a battery is the most accurate way of determining the available capacity. This operation will show the available autonomy time, general state of health of the battery and the effects of aging. The results of the discharge can also be used to estimate the remaining life span for normal aging characteristics. However, an on-line discharge test carries some risks:a) risk of system failure should an individual battery fail suddenly during the test;b) risk of reduced standby time should the public power supply fail before the battery is fully recharged, i.e. when it is empty. However, an on-line test could be programmed to take place when traffic is light or during planned system down times, and data can also be gathered and compared over a period of off-time from real emergency discharges. BACS measures and indicates the battery capacity once per second during discharge, and such a discharge test can be carried out without the risk of unnoticed damages of cells/batteries
Impedance
- Ohmic Resistance and/or Electrochemical Impedance – With BACS, this is indicated by the “RI” reading; the trend line as indicated in the BACS VIEWER shows the expected lifetime.
- Resistance: AC/DC resistance or conductance can be used to monitor the state of health of a cell and to follow its aging profile. AC/DC resistance or conductance monitoring can therefore not accurately determine when a product has reached a precise capacity value, e.g. 80 % of nominal, but can be successfully used to find faulty cells before they cause a battery failure. In addition, by plotting AC / DC resistance values against time to produce a broad aging profile for cells or batteries in service, it may be possible to predict when cells need to be replaced. AC/DC resistance monitoring can therefore be used to derive a life profile by plotting the change in AC/DC resistance or conductance against time, as a cell ages. AC/DC resistance should only be used on fully float-charged cells to achieve good results. BACS: The difficulty is that in given high voltage string applications (UPS), the cells/blocks tend to deviate from the ideal float charge voltage and differences of 2V and more are frequently found within the string. Such a situation makes it impossible to compare the AC/DC resistance measurements under float charge. BACS balances the voltage differences so that all cells/batteries are equal, not differing more than 0.01 Volt from one neighboring cell/battery to the next. This allows for a comparison between the AC/DC resistance values, and makes the use of such measurements useful for diagnostic procedure.
- Base Line RI: If the test is an initial test, the AC / DC resistance or conductance is stored as the initial AC / DC resistance to be used later as a base against which to compare battery performance as the battery ages. BACS offers freely configurable threshold settings for RI resistance, based on absolute values in mOhms, based on Dynamic values, or based on a given set of “Base Line” values, depending on what best suits the installation.
Temperature
- Temperature impacts on the battery capacity: Available battery capacity is influenced by the battery temperature. In order to accommodate for various temperatures (10 °C to 30 °C), a capacity compensation of 0,6 % per degree Celsius is normally applied. For high rate discharges, the capacity compensation coefficient can be considerably larger. BACS’ Battery Capacity display is based on this capacity compensation per degree Celsius and adds this factor into its calculations of Battery Capacity.
- Temperature influence on battery life span: The battery life span is normally specified at 20 °C (for lead acid) and is influenced by the operating temperature. Elevated temperatures lead to a shortening of useful battery life. For a constant temperature increase of 10 °C, the life is expected to be reduced by approximately 50%. Battery lifetime can be predicted using Temperature profiles, but such a method is very unprecise if no other aspects are taken into calculation. BACS records the battery temperature over the long-term and the average temperature is shown so that the user knows what the life-span for his batteries should be.
- Temperature influence on Battery self-discharge: A given battery self-discharge is influenced by the temperature and increases progressively in relationship to an increase in temperature. BACS shows the trend of the battery voltages over time; also measured is the historical Equalization/Balancing activity in %. If balancing is indicated at 0% but the charger is running, this would indicate either that the battery breaker may be open and the self-discharge is draining the battery – OR – the temperature is too high so that the self-discharge is greater than the current from the charger, which has to be altered to compensate the behavior of the temperature increase or aging effect of the batteries.
- Temperature influence on Battery charge current: At a given constant voltage, the float current passing through a fully charged stationary battery increases progressively with increasing battery temperature. BACS shows this increasing current and balances this out within the limitations of the system. Typically, this is enough to avoid battery damages because the UPS or charger automatically decreases the charge voltage (and the current) if the external sensor reads higher temperatures.
- Influence of ripple currents on battery temperature: Ripple currents generate heat within the battery resulting in an increase of battery operating temperature. BACS monitors and indicates AC and DC ripple currents, allowing for corrective action before such an effect causes an increase in battery temperature.
- Temperature differences due to a poor design of a battery installation can cause battery faults: In an installation where a battery is mounted in several tiers, there may be a battery temperature difference of several degrees between the upper and the lower units. Such temperature differences cause considerable temperature variations within the cells; where such a difference of more than 5°C exists, this may result in the reduction of the battery’s electrical performance. BACS is able to balance the voltages within the string, whether the voltage differences come from the poor layout or from chemical differences within the batteries. This ensures that performance reduction owing to temperature differences due to poor design in the battery layout is otherwise negated.
- High temperature differences for a time period > 24h can cause a thermal runaway: In the event of a persisting average temperature difference between the battery temperature and the ambient temperature, there is a risk of thermal run-away or other faulty functions in the battery. This characteristic applies only to the float charge operation and does not apply to the discharge operation. BACS: If the charger is setup correctly and BACS can balance the voltage differences due to thermal or electrical differences, the risk of such a thermal runaway under float conditions can be dramatically reduced or avoided entirely.
- High temperature: In order to reduce the risk of damages or faults as a result of sustained temperatures outside of manufacturer recommendations, a battery installation should be provided with appropriate cooling. BACS cannot prevent overheating of batteries due to room ventilation issues, but BACS can warn the user about such conditions and, if connected to the appropriate automation protocols, automatically switch on AC or trigger to open windows, fans, etc. to solve the situation.
- Real Cooling Demand - BACS: The cooling demand is determined by the difference recorded by BACS; it generally increases with age due to the increased current consumption during trickle charging and thus indicates an increasing risk of thermal runaway.
Battery Current
- Float current – AC component (super-imposed ripple current): The ripple current (AC component) is generated by the charger and/or by the load (e.g. inverter) and is super-imposed to the DC float current. This ripple current does not contribute to the battery charge; it only generates additional heat. A high super- imposed ripple current and a DC current near zero will lead to discharge and deterioration of an effected lead-acid battery. It should be noted that the float current at the end of life of a VRLA battery doubles in comparison to a new battery. BACS: Such an increase of the float current can be visualized with BACS and can trigger an alarm. Alarm levels for DC float currents can be set within the BACS configuration to avoid a malfunction of the battery due to increased water loss, excessive shedding of active material or the promotion of internal short circuits and excessive heat evolution, which in the end may cause thermal run- away.
- Maximum ripple current: Under float conditions, the super-imposed effective ripple current at frequencies >30 Hz should be limited. Appropriate precautions should be taken in order to avoid dangerous voltages and short-circuits at and through the sensing leads. Fast fuses or current-limiting resistors shall be inserted into each sensing lead. BACS is the only BMS on the market with 2 high voltage fuses featured within the sensing leads. Flame retardant/low smoke and fume or acid resistant insulation may under certain circumstances be required for the sensing leads. BACS utilizes halogenfree cables and fire retardant material for housing and components to avoid damages caused by such dangerous voltages – except the fuses – and can disconnect itself from the system to trigger alarms about the blown fuse and ripple voltage.
- Load share current: Current Sensor Values: Where two or more batteries are operated in parallel, the terminal voltage of each battery shall remain equal during a discharge (assuming connectors of equal length and volt drop) and for batteries of the same performance and AC / DC resistance, i.e. same type, rating, age and design, they shall also share load current. A battery containing low performance cells will have a lower voltage discharge profile than a healthy battery and, when connected in parallel with a healthy battery, will supply a smaller percentage of the load current. Therefore, where similar batteries are operated in parallel, load share can be used to indicate poor performance by comparing the difference between the maximum string current and the minimum string current, as a proportion of the overall load current. BACS shows current values per string and allows to set thresholds if these values get imbalanced; should such an imbalance occur the operator can thus be informed accordingly.
- Energy Flowthrough – this figure is measured through use of the new BACS Current Sensor Type CSHxxxF and CSHxxxD. The BACS Current Sensor in tandem with the measurement data of the BACSVIEWER is able to display the trend line of the aging battery or cell.
Battery Health and Sustainability
- Ongoing Development of the Self-Discharge Rate – this can be identified by the otherwise naturally decreasing autonomy time of a given battery or cell. The older the batteries become, the higher the self-discharge rate. To determine the exact development curve, the trickle charge must be switched off while the given cell or battery is in the fully charged state; the BACS and SMARTLOGGER, SMARTBATTERY measured values will show the self-discharge rate after a few days. This must be compared with the self- discharge rate in new condition.
- Date of Battery Manufacturing and Commissioning – this is defined and archived for up to 10 years during commissioning of BACS and SMARTLOGGER and SMARTBATTERY.
- Data Access – clear unobstructed access to the aforementioned parameters be available for analyzation at any time in order to assess the residual value of the battery, to facilitate battery reuse, repurposing or remanufacturing, or to make the battery available to independent aggregators operating virtual power plants in electricity grids. BACS, SMARTLOGGER, SMARTBATTERY provides the data in various formats to make it analyzable by recyclers.
- Long-term Data Recording as applies to Storage and Transport Conditions – the storage and transport conditions of batteries must also be recorded in order to be able to reprocess batteries or to document hidden damage caused by errors or otherwise faulty performance of these processes. Therefore, the manufacturer is required to ensure that the examination, performance testing, packaging, and shipment of batteries and their components are conducted in accordance with appropriate quality control and safety instructions. The SMARTBATTERY or SMARTLOGGER from GENEREX provides the desired long-term data – from “the cradle to the grave” – thus allowing for precise control of operating and storage conditions for the complete life cycle of a given battery unit.
- Documentation Availability – in order to prove that a battery is no longer waste, documentation must be provided for indicating the health and functionality of a given battery or cell. The economic operator who wants to perform the recycling must be provided with a document for the evaluation or testing of the aging condition. SMARTBATTERY, SMARTLOGGER and BACS record and subsequently provide the required information for documentation.
- Battery Passport – the EU requires that by January 1, 2026, every industrial battery and traction battery placed on the market must have an electronic identification file ("battery passport"). Each battery will have its own battery passport with individual identification and data on the producer, battery type, batch or serial number, date of manufacture, date placed on the market, chemistry. The battery passport is linked to the information on the basic characteristics of each battery type and model, which must be stored in the data sources and made available online. BACS, SMARTLOGGER and SMARTBATTERY are already able to provide all the data required for a "battery passport" in a permanent and accessible format.
Conclusion
The above comparative analysis ought to indicate that BACS, the leading European and North American- made battery management system in combination with SMARTLOGGER and SMARTBATTERY, stands ready to fulfill any and every need required by European and International regulatory publications. As a ready-made solution, our products can “fill the gap” in your product portfolio – especially in light of the upcoming requirement for a BMS on each and every stationary battery installation!
To discuss a cooperation today, please contact us at your convenience either by email (sales@generex.de) or by telephone at +49 (0)40 2269291-190.
James May
Previous Article
Next Article