NERC PRC-005 Standard for Battery Technicians in den USA
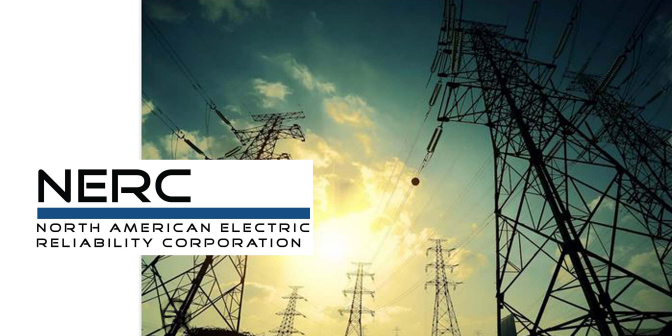
The NERC PRC-005 Standard for Battery Service Engineers
Clearing up common questions regarding the NERC PRC-005 Standard, and why BACS makes the life of a Battery Technician easier while also reducing the overhead costs of the end-user!
As a nonprofit regulatory corporation based out of Atlanta, Georgia, the North American Electrical Reliability Corporation (NERC) has provided the framework for maintenance standards used in the electrical utility industry and has been a driving force for the “Automated Battery Management and Maintenance” fields. NERC is the quintessential Standardization Institute in North America, and most the standards passed on their behalf have found their way into the European Standards by way of parallels like DIN, IEC Norms. In Europe, Battery Management as an independent concept in relation to Battery Monitoring is still relatively new and not as mature as in North America – the assumption can well be made that what happens on one side of the Atlantic will eventually happen on the other.
The Utility-specific standard (PRC-005-6) establishes the varying requirements for maintenance activities and intervals that result in an on-site visit. The specific maintenance activities stipulated are based on whether the battery accords to a Vented Lead Acid (VLA) or Valve Regulated Lead Acid (VRLA) design.
The following are the maintenance activities which a given battery technician would be expected to perform according to this standard:
- Verify DC Supply Voltage and Float Voltage
- Verify Battery terminal connection resistance
- Verify Battery Intercell Connection resistance
- Measure internal Ohmic Values and Cell conditions
- Inspect for unintentional grounds and the physical condition of the battery rack
- Verify Battery Continuity
- Inspect Electrolyte level
That’s an honest bit of work! Especially if the technician is expected to perform such measurements and tests “by hand”, individually, with each battery within the given system! Endusers and service engineers alike generally seek ways in which the overall effort / cost / time required can be reduced; this search is illuminated by the further NERC stipulation that no such periodic maintenance activities are required if State of Health (SOH) monitoring and alarm systems are utilized!
This stipulation on behalf of NERC is dramatic in that it further supports the broader usage case for BMS systems like our own BACS Battery Management System, which already has an established reputation for extending and protecting the value of a client’s battery system investment. That such a BMS can in parallel reduce the overall maintenance requirement for such a given system through this NERC stipulation only further hammers home the logical argument.
Although the use of a BMS can reduce the Battery Service maintenance costs dramatically, there nonetheless remain minimum standards for regular maintenance intervals ranging from four, six, and eighteen months, depending on the Battery Type, regardless whether a BMS is in use.
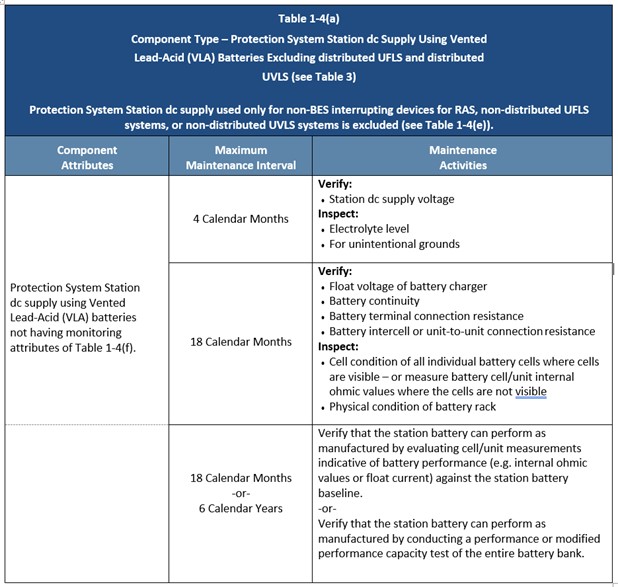
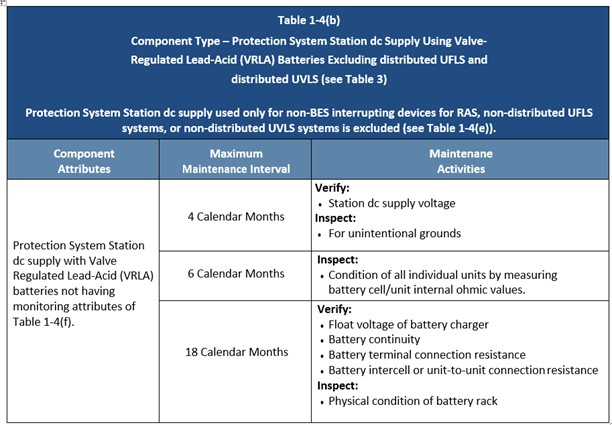
As you can read from the list above, most maintenance items are relatively straightforward. Still, some maintenance items, such as Battery Continuity and Battery terminal/Intercell connection resistance, have come into question. Therefore, in October 2015, NERC also released a Supplementary Reference and FAQ document (NERC) which helps clear up any confusion the user may have on these items. Let’s unpack some of those items:
Battery Continuity
This maintenance item must be performed every 18 months. The purpose therein is to identify potential breaks in connection along the battery’s current path which could potentially result in or cause critical power loss. As such, a given BMS is required to provide a method of measuring the battery continuity of the string. Some methods prescribed in the supplementary reference include: measuring float current on the battery string, discharge testing, and measuring the internal ohmic values of the jars or cells.
Most BMS products in the marketplace today have some variation of ohmic value measurements; generally speaking, the BMS provides for such a measurement on a daily schedule, putting the user in NERC compliance for this maintenance item. The NERC Supplementary Reference states, “Internal ohmic measurements of the cells and units of lead‐acid batteries (valve‐regulated lead‐acid (VRLA) & vented lead‐acid (VLA)) can detect lack of continuity within the cells of a battery string; and when used in conjunction with resistance measurements of the battery’s external connections, can prove continuity. Also some methods of taking internal ohmic measurements, by their very nature, can prove the continuity of a battery string without having to use the results of resistance measurements of the external connections. (pg. 80)”
Generally speaking, we at GENEREX agree only partially with this stipulation, since most BMS provide an ohmic value without respect or relation to the measured voltage – which leads to misinterpretations at best, and the masquerading of failures at worst. When measuring impedance on an overcharged block without also comparing a “baseline” voltage across multiple blocks, the impedance otherwise appears “normal”; in active comparison to adjacent batteries under an equalized/harmonized base voltage, the individual impedance of the overcharged block shows a clear difference and can thus be considered accurately. BACS, as a provider of such balancing/harmonization of individual unit voltages, provides this key framework.
Terminal/Intercell Connection Resistance
Used to ensure that there aren’t any loose connections between the jars or cells, this maintenance item also needs to be performed at least once every 18 months. A loose connection can cause excessive heating during a discharge or voltage drop, disrupting the battery’s continuity.
Some BMS manufacturers measure the intercell as an individual reading or as a part of the battery ohmic value. In any case, it’s been disputed whether or not the user must display a separate intercell value to comply with NERC. According to the NERC Supplementary Reference: “There are test methods presently that can read post-termination resistances and resistance values between external posts. There are also test methods presently available that take a combination reading of the post-termination connection resistance plus the intercell resistance value plus the post-termination connection resistance value. Either of the two methods, or any other method, that can show if the adequacy of connections at the battery posts is acceptable. (pg. 83)”.
Bringing the point home: BACS is a ready-made NERC Solution
As such and based upon both the NERC standard itself as well as the additional Supplementary Reference, The BACS Battery Management System is the ideal for any stationary battery system! As the quintessential Management system – as opposed to the more common and far less comprehensive “Monitoring Only” BMS found elsewhere on the marketplace – BACS provides for continuous state of health monitoring and management of your batteries. Most importantly, BACS battery management system boasts the required metrics and reporting functionality to keep the user within NERC compliance.
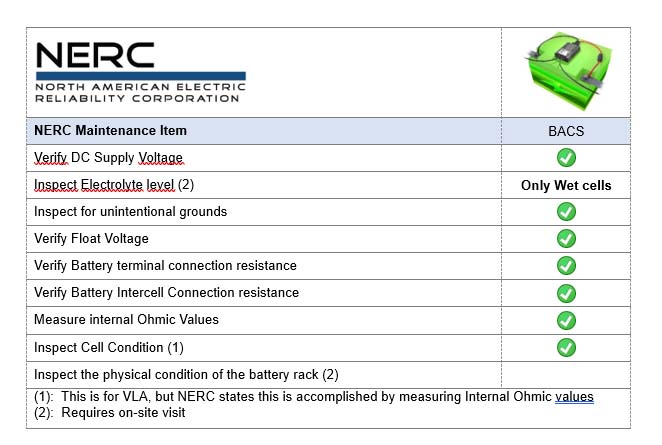
Fundamentally, a BMS system which meets all of the stipulated requirements makes the user’s job a lot easier; what’s more, by providing the framework for a “passive compliance” to the bulk of NERC standards and preventing the need for frequent, tedious site visits and maintenance appointments, use of a BMS such as BACS also results in an overall dramatic reduction in operating costs!
Once again, BACS rises head and shoulders above any other competing BMS system on the planet. Whether protecting your battery investment, extending your battery asset usage duration, or preventing any number of additional overhead costs such as maintenance and “hands-on” monitoring, BACS is the quintessential definition of a “sound investment”!
References:
Back to
Next Article