BACS für use in harsh Industrial Environments
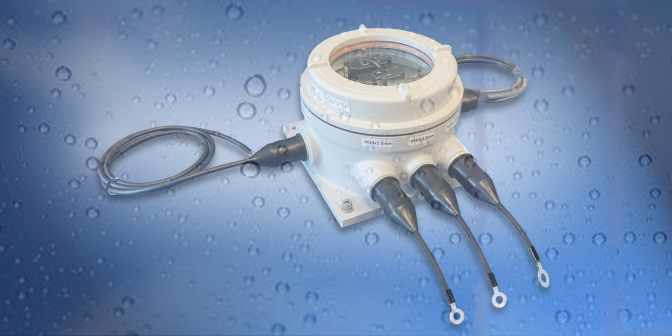
BACS for outdoor installations
The availability of BACS as an ATEX version also solves another application problem - BACS for outdoor installations or in harsh industrial environments.
The Zone 2 ATEX housings are not only explosion-proof, the hermetic sealing of all electrical components by the ATEX housing means that BACS can even be used “under water” – or in corrosive environments – which is much more common as an application for batteries an operation under water….
The reason for using an ATEX housing in harsh or aggressive atmospheres is often the constant conditions on site. BACS is used in railway tunnels, ships, submarines, oil and gas industries, military installations and many other applications where it is often impossible to maintain the operating conditions for which electronics are designed. Precisely because lead batteries are almost exclusively used in such environments (due to the lower risk of fire), such locations for BACS are more the rule than the exception.
However, a “standard” BACS system is also significantly safer electrically than any other BMS on the market as concerns electrical safety, such as protection against contact and prevention of overheating or generation of sparks. Of course, this is not enough for an ATEX environment, but it is also not enough to operate the product in most unclean environments. Just because BACS is electrically safer than other products on the market and is used in ATEX environments at the user's own risk does not mean that the system can be "attributed" to the expected robustness for industrial and outdoor environments.
In fact, the “robustness” of BACS reaches its limits as soon as the environments also contain corrosive atmospheres – for example an installation in a much more “aggressive” atmospheric environment in which the natural corrosion processes could be accelerated.
We found several use cases where BACS was installed in environments that were otherwise within the BACS specification for temperature and humidity, but where, for example, frequent temperature changes resulted in condensation.
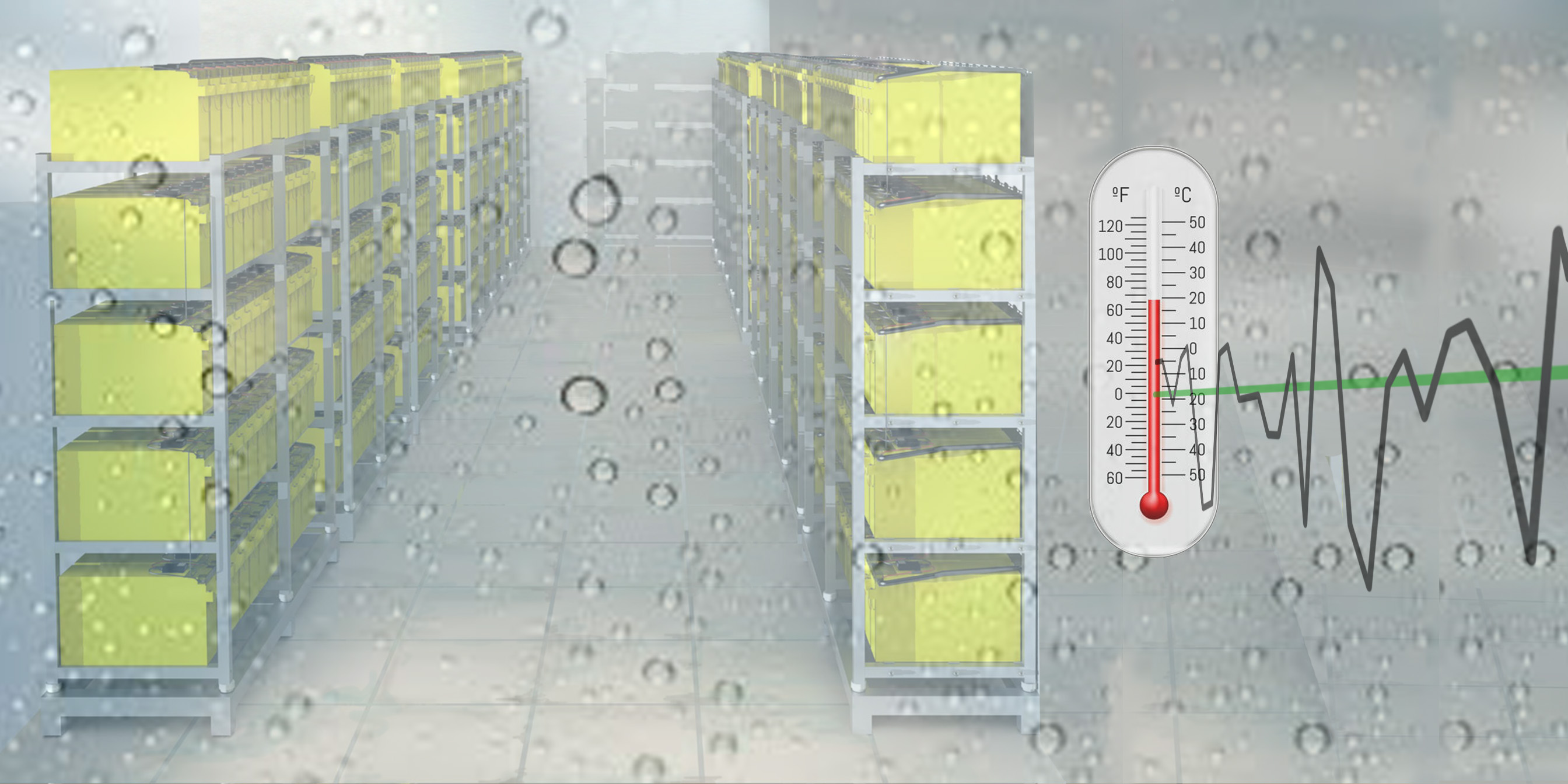
The result of condensation in potentially contaminated rooms (sulphur, salt crystals) creates an aggressive atmosphere and thus corrosion on all exposed parts, including in long-term operation on parts protected by protective varnish. This sometimes led to the complete failure of the modules and cables used.
The BACS modules and cables sent to us for examination showed significant signs of corrosion as shown in the picture. Even without climate control in other harsh industrial environments, such traces of corrosion after only a short period of use in the field were previously unknown to us in Europe and the USA
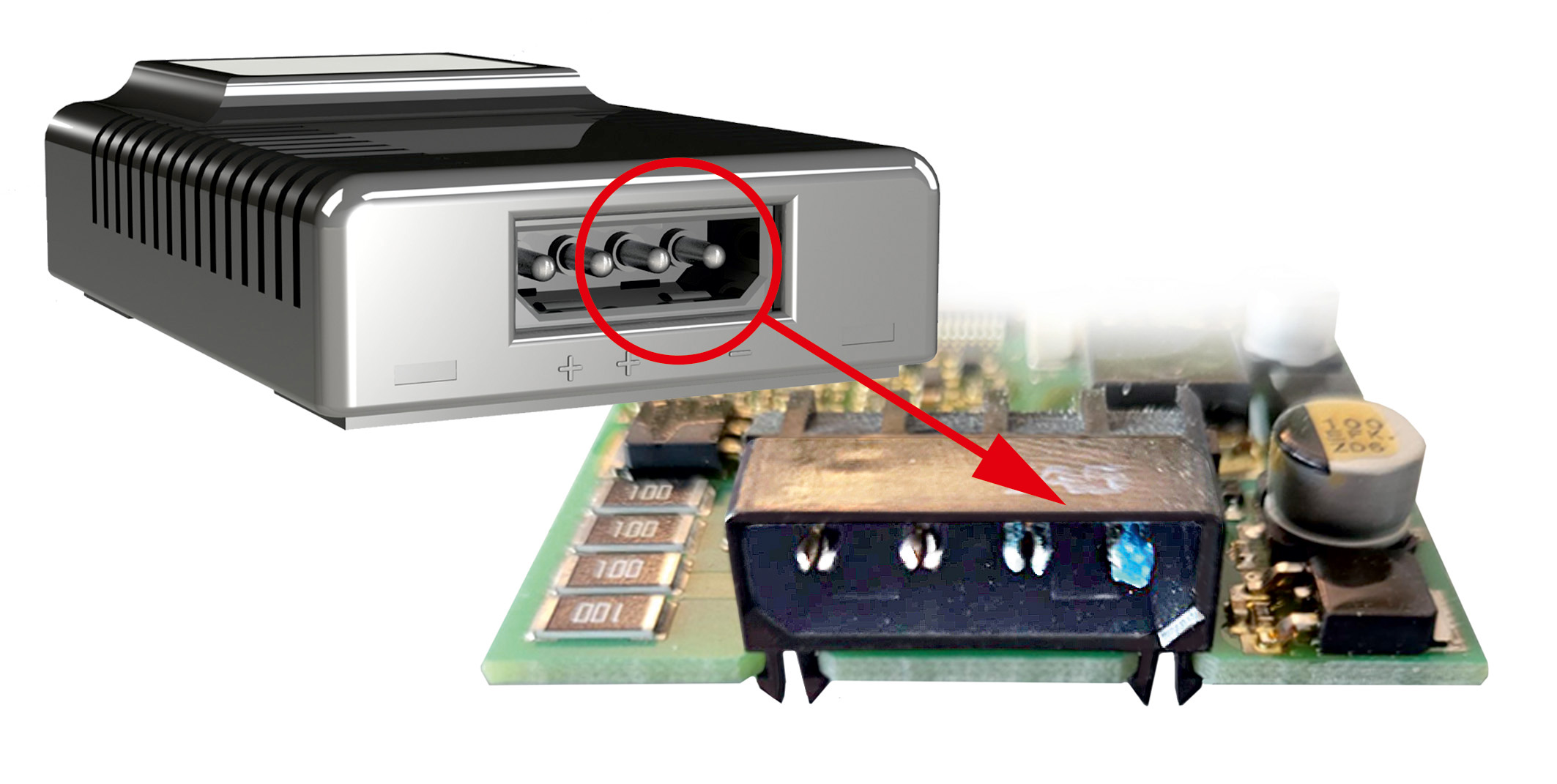
Our investigations have shown that the BACS modules (and all connecting cables) were contaminated with a basic electrolyte.
The first question was: How does electrolyte get into a BACS module if the module is located above the battery filler neck?
Electrolyte leaks in battery rooms are rare and usually only limited to wet cells. Most such leaks are of no major consequence and usually only occur in new batteries that have never been through a cycle (discharge/charge). This is known to most battery technicians, which is why at least one discharge is carried out during picking so that the electrolyte level can then be checked and possibly corrected. If the electrolyte level is set correctly after the cycle, leaks due to overfilling should no longer occur. If electrolyte leaks again later, this should not cause any damage because wet cells should always be installed at ground level or, in rack installations, there is a collecting tray for electrolyte under each level. This prevents leaking electrolyte from dripping directly onto the batteries underneath.
In the case in the picture above, however, the corrosion could also be found on the BACS modules, which were arranged at the very top of the rack, where no contact could actually take. Nevertheless, the modules and cables were significantly contaminated and corroded even on the first level.
Use in higher temperature ranges has little influence on BACS. However, if there is a connection with high humidity and changing temperatures, condensation results. This also has little impact in temperate zones. The protective varnish on the BACS board protects against dust and normal humidity. However, this only applies to the areas covered by the paint. If the BACS modules are constantly exposed to increased humidity, this causes corrosion on the components that are not protected by the paint (cable sockets, addressing switches, temperature sensors). This corrosion can be gradual and not noticeable for years, as demonstrated by more than 10-year-old BACS installations in European, American and Asian battery rooms.
However, the speed of the corrosion processes changes significantly if moisture is repeatedly created through condensation in a room with battery acid residue!
Changing temperatures and high humidity lead to condensation. During each condensation process, electrolyte crystals are dissolved in the surrounding area and distributed through the air in the room. These electrolyte salts, dissolved in the humidity, create an aggressive environment and therefore significantly faster corrosion on all exposed metallic parts, much more than in identically contaminated rooms WITHOUT such condensation.
Almost all battery rooms with wet cells have been contaminated with electrolytes over the years, which is not a problem in temperate atmospheres. However, if a metallic surface that is contaminated through the air becomes “wet” through accumulated moisture, it will “rust”, and the more moisture and heat that is added, the faster it will do so.
This corrosive mixture of humidity and electrolyte destroyed the addressing switches in the BACS modules we found, and later also destroyed LEDs and other components, and ultimately led to a total failure of the BACS module.
Such cases of corrosion on BACS modules are not found in data centers or other wet cell battery rooms that have normal temperature and humidity levels, but in tropical regions especially where NiCd wet cells are used due to the expected temperatures.
Typically, wet cells in tropical environments are delicate to handle because when the cells are refilled with distilled water, a particularly strong foaming effect occurs. Due to this foaming, there is usually significantly more electrolyte in the room than in identical rooms without high humidity. The adjacent picture of an older battery installation shows that humidity makes a difference: Significant acid damage can be seen on the floor of the battery room. Although the room is significantly contaminated with electrolytes, the BACS modules show no signs of corrosion damage even after being used there for over 15 years!
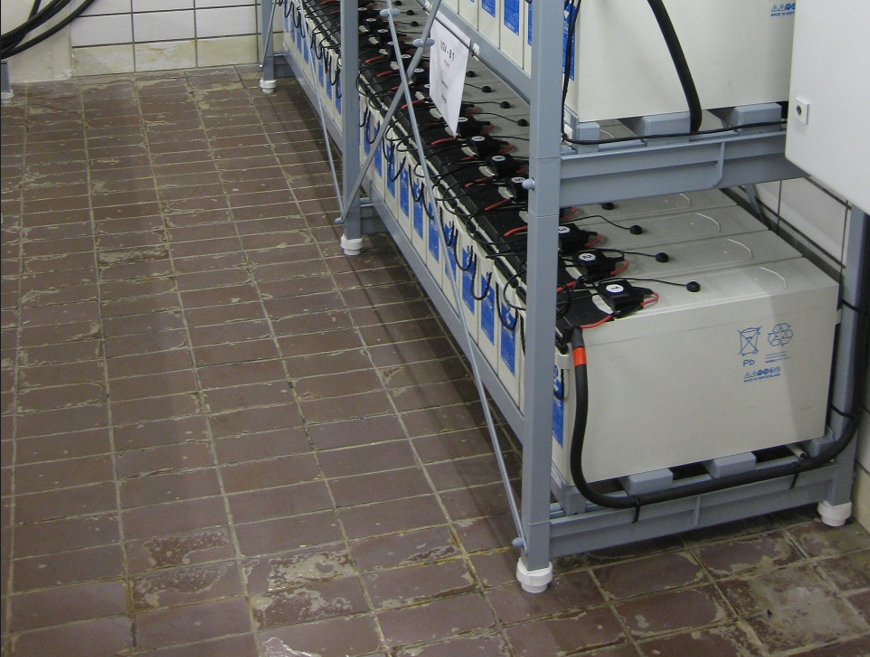
The influence of temperatures on battery rooms is inevitable to a limited extent, but as long as lead batteries or NiCd are used, it is not particularly problematic. This is one of the main reasons for using these battery technologies in such places.
To prevent damage to BACS or other electronics in such battery rooms, the room air should at least be as dry as possible. Air conditioning systems regulate this automatically, but even normal, unconditioned ambient air does not cause any problems if condensation is avoided.
But if BACS is used in tropical regions - without air conditioning - and wet cells are also used, in which, due to the high temperatures, they often have to be refilled with electrolyte or water to compensate for evaporation, then the probability is high that such “Foaming” occurs in the surroundings – and then an increased corrosion process will begin.
We therefore recommend that if condensation cannot be prevented (for structural reasons):
- Do not use wet cells as batteries: The use of wet cells, especially nickel cadmium cells, have a high level of robustness at existing elevated temperatures. However, the advantage turns into a disadvantage as soon as the cells are used in environments with additional high humidity. Many customers have recognized this and are now using “pure lead VRLA batteries” or, if there is a lack of space, batteries with lithium titanium oxide instead of wet cells based on lead or NiCd-based batteries. Pure lead batteries achieve almost the same temperature ranges as specified for NiCd batteries, with significantly lower material and service costs. The fact that such VRLA batteries also release almost no electrolyte is another advantage for problematic environments.
- The BACS ATEX module:If it is unavoidable to use wet cell batteries and expose the sensors to corrosive environments, the new BACS ATEX module provides the optimal solution and ensures decades of operation without corrosion and the resulting high operational reliability.
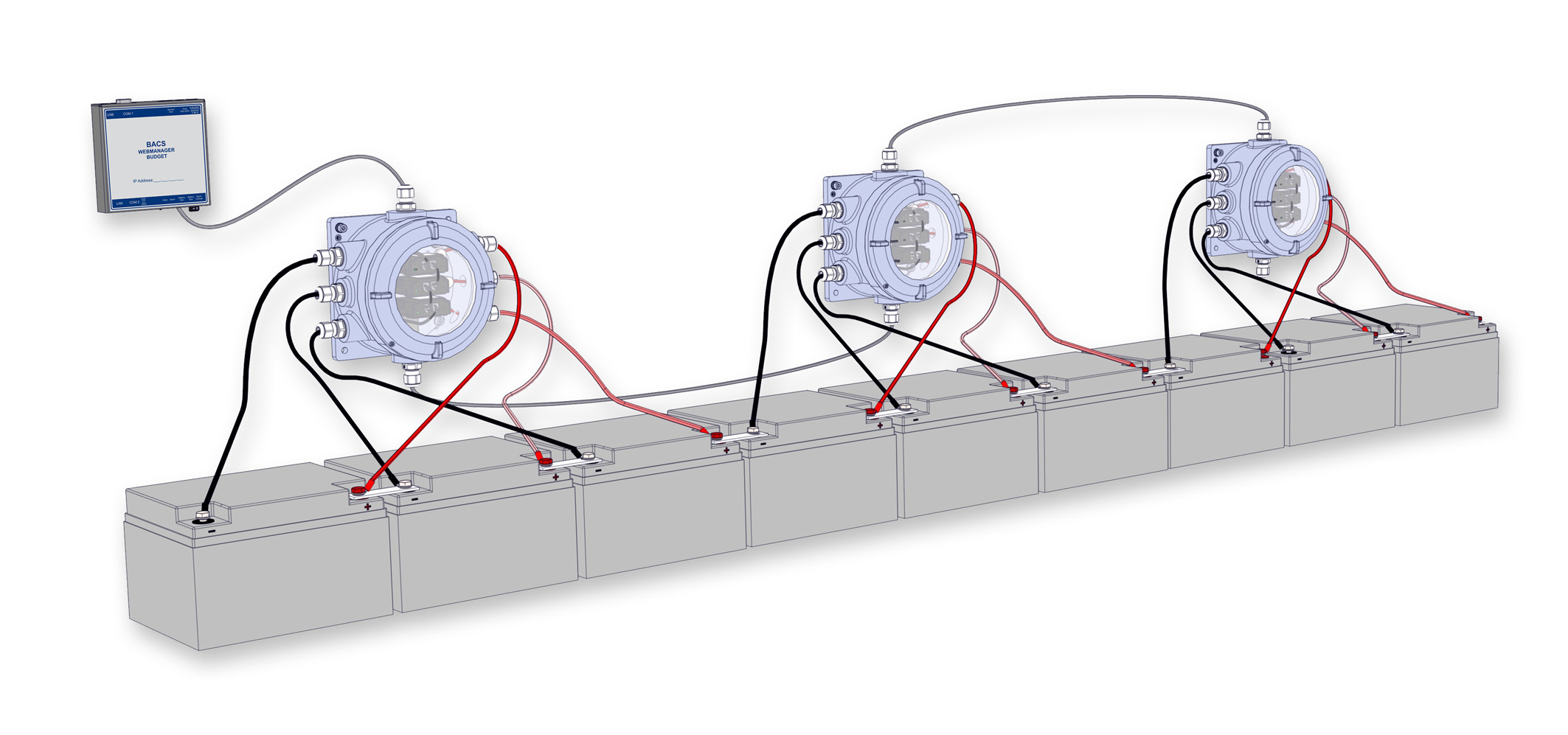
Back to
Next Article